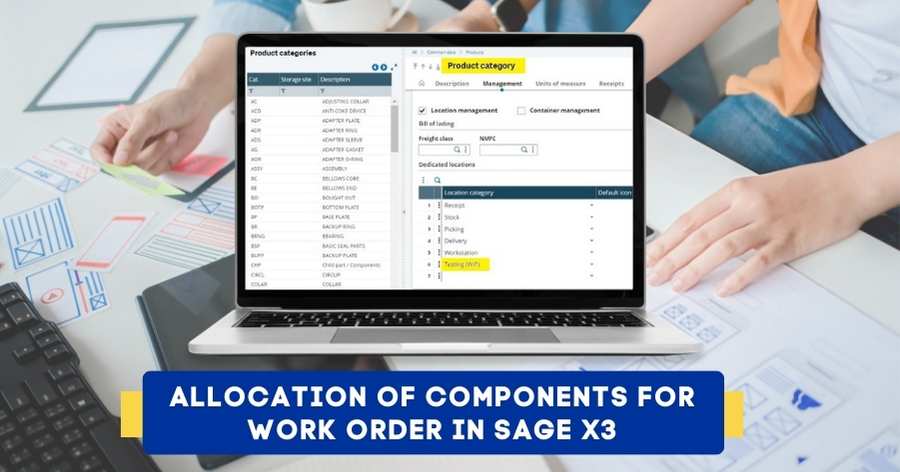
Allocation of Components for Work Order in Sage X3
Steps to Allocation of Components for Work Order in Sage X3 This blog refers, how to configure the work order allocation rules based on the
Steps to Allocation of Components for Work Order in Sage X3 This blog refers, how to configure the work order allocation rules based on the
Sage X3 is one of the most popular ERP Software used across the world. It offers an intuitive design, visual navigation, a customized dashboard, and
What is RCM? In this blog, we will walk through how to set up RCM taxes in Sage X3 for purchasing transactions. By the end
Project Creation Includes 3 Steps:- Creation of Project Creation of Task Planning Creation of Cost Structure Creation of Project Steps for the Creation of Project:-
What Is Multiple Step Operational Loss? We can define scrap loss for each raw material as well as operation loss against each step of our
Asset disposal is the process of removing a long-term asset from a business’s accounting records, either by scrapping or selling it. In the Sage X3
If a product is not sold on time and is just lying around the warehouse. Then mostly the product cost is revised as per the
Steps to resolve “Table is Full” error in Payment Proposal Screen in Sage X3 If you encounter the error message: “Table is full: All the
How to resolve the error @X3.TRT/GLOBB1$adx (572) Error 8: Index Incorrect DEPSTA(-1) in fixed asset depreciation calculation screen When we change the depreciation method from
In many businesses, customers often request a sample of the product they are interested in before making a purchase decision. To attract prospective customers, companies
Fill in the details below and we would be glad to help you.